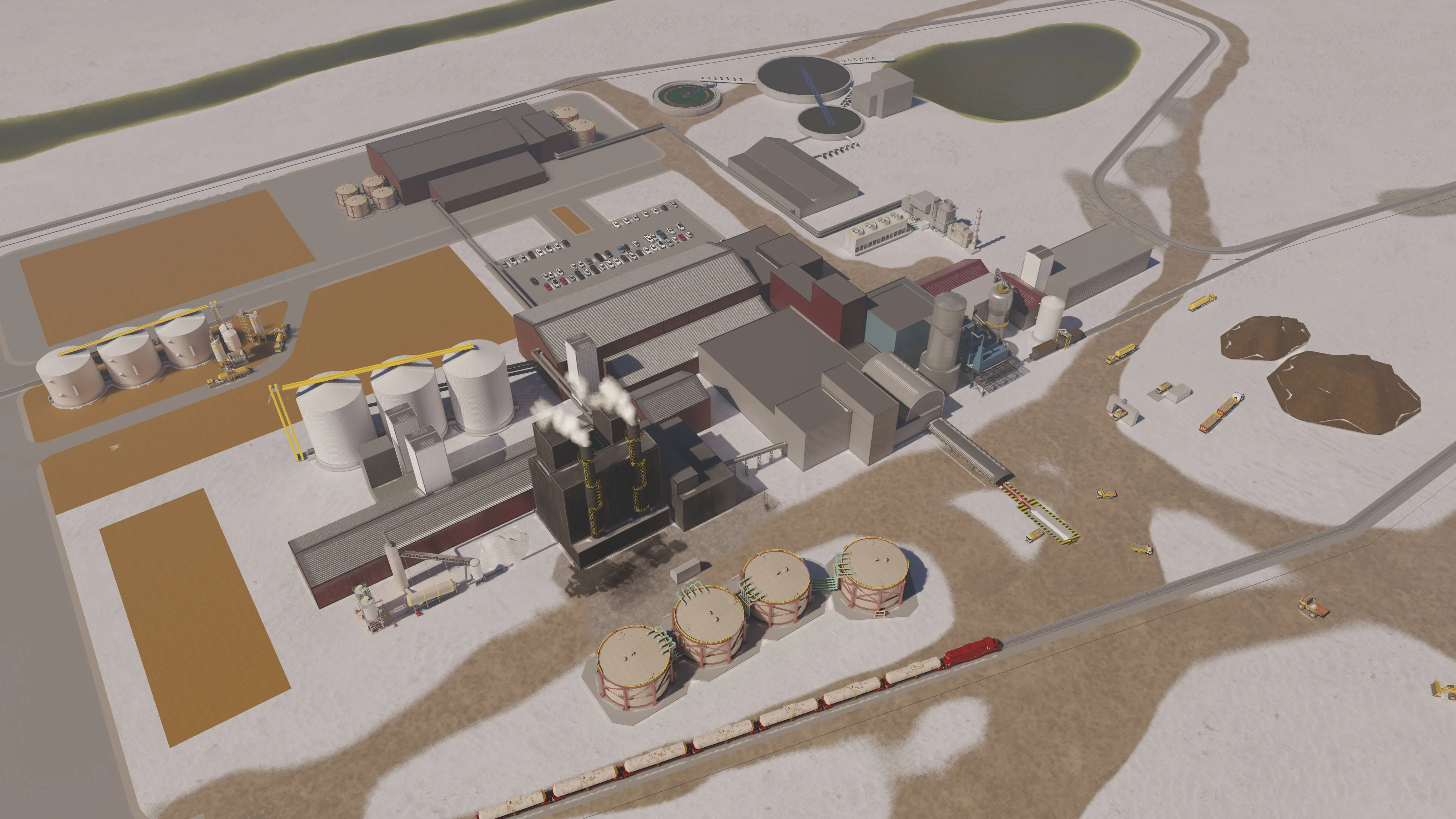
Sugar Beet Process Solutions
Cleaning / Extraction
Purification
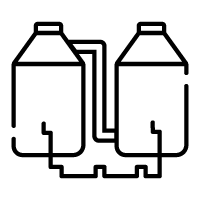
Evaporation
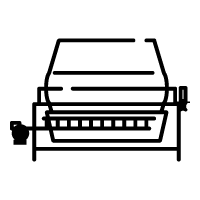
Vacuum Pan, Crystallization, Centrifuge
Drying/Storage
Lime Plant
MDS Plant
Pulp Drying / Pulp Press Spindle
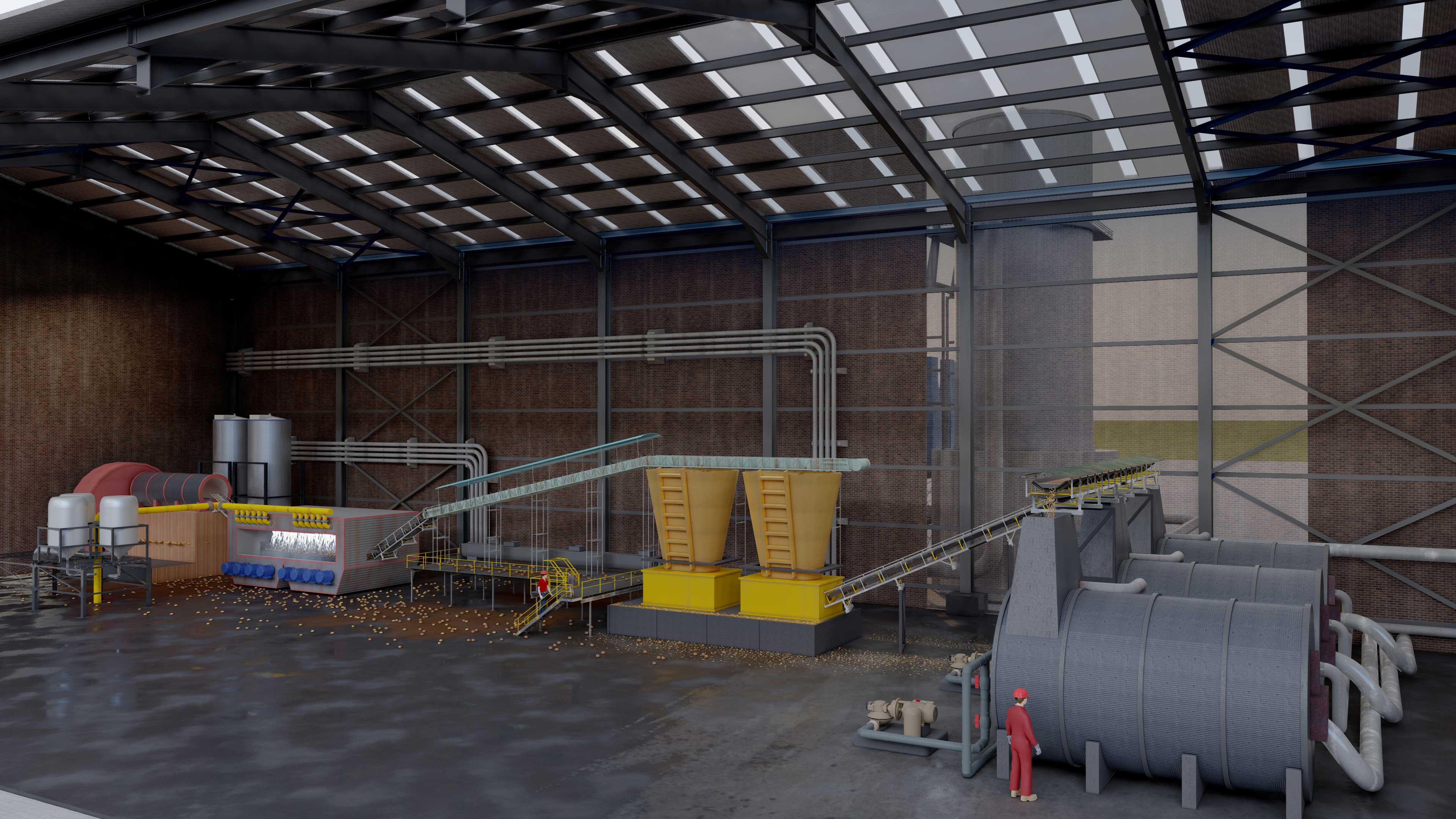
Cleaning / Extraction
The beets are received and washed to remove mud, rocks and sand, and dropped into a hopper to be sliced into cossettes. The cossettes are sent to the diffuser to extract sugar solution named raw juice.
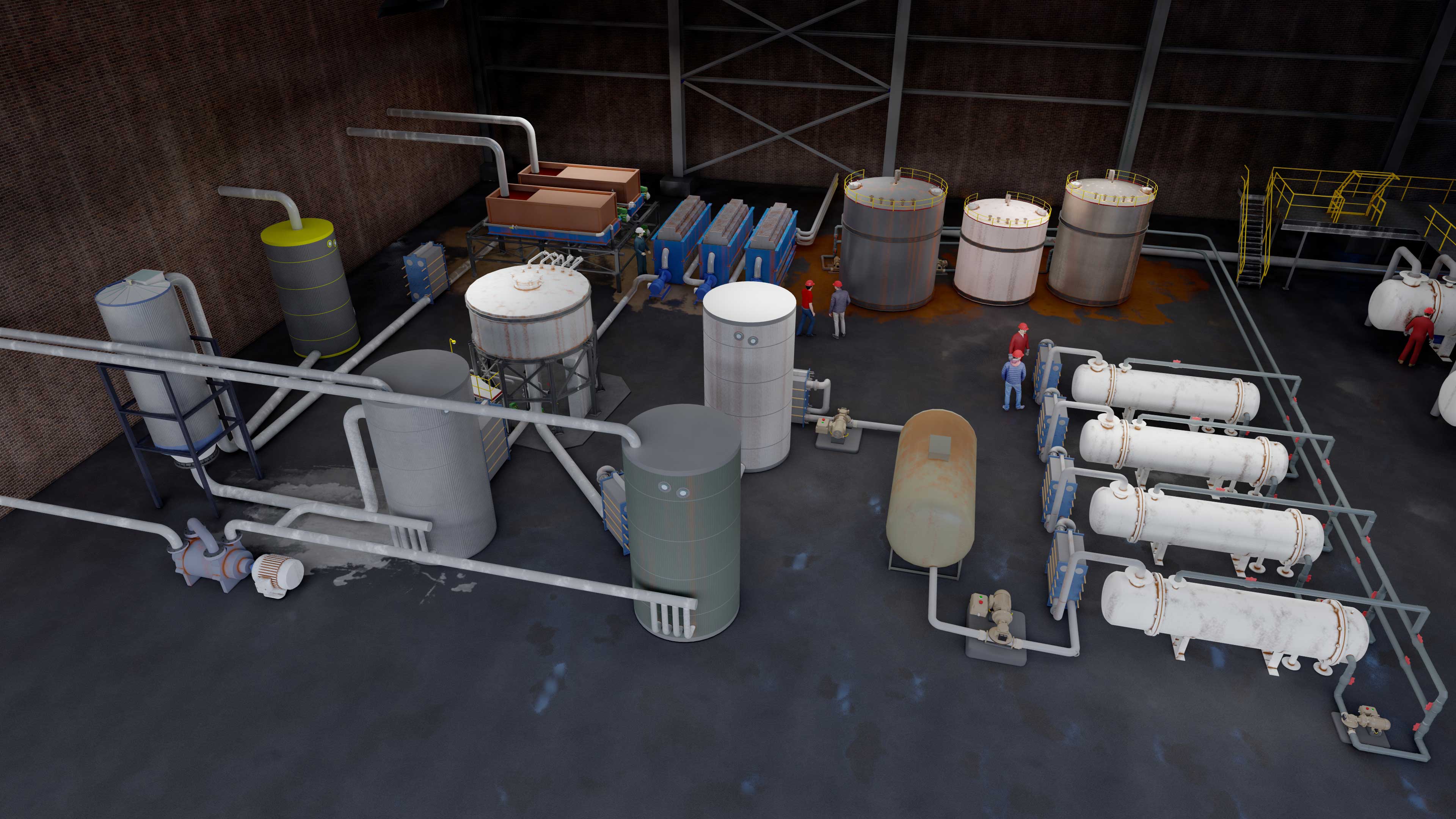
Purification
Raw juice is moved through various stages of purification and filtration to remove impurities and other non-sugars. The juice then moves to the evaporator supply and is named thin juice.
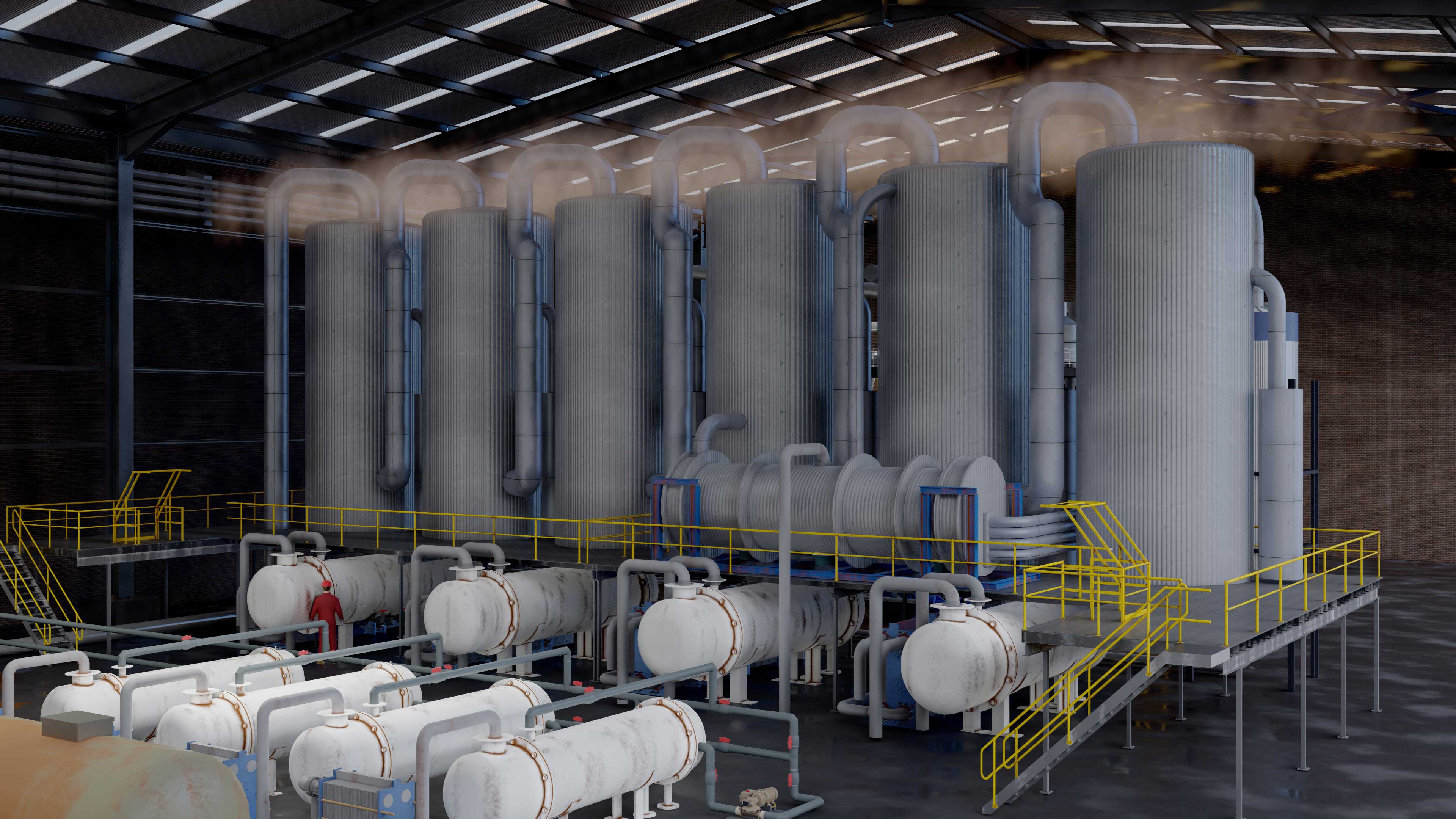
Evaporation
Thin juice with 13%-15% sucrose moves through multiple evaporators heated by exhaust steam to remove excess water until it becomes thick juice with 65%-70% sucrose.
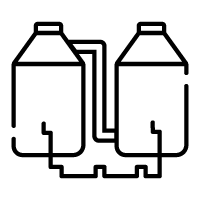
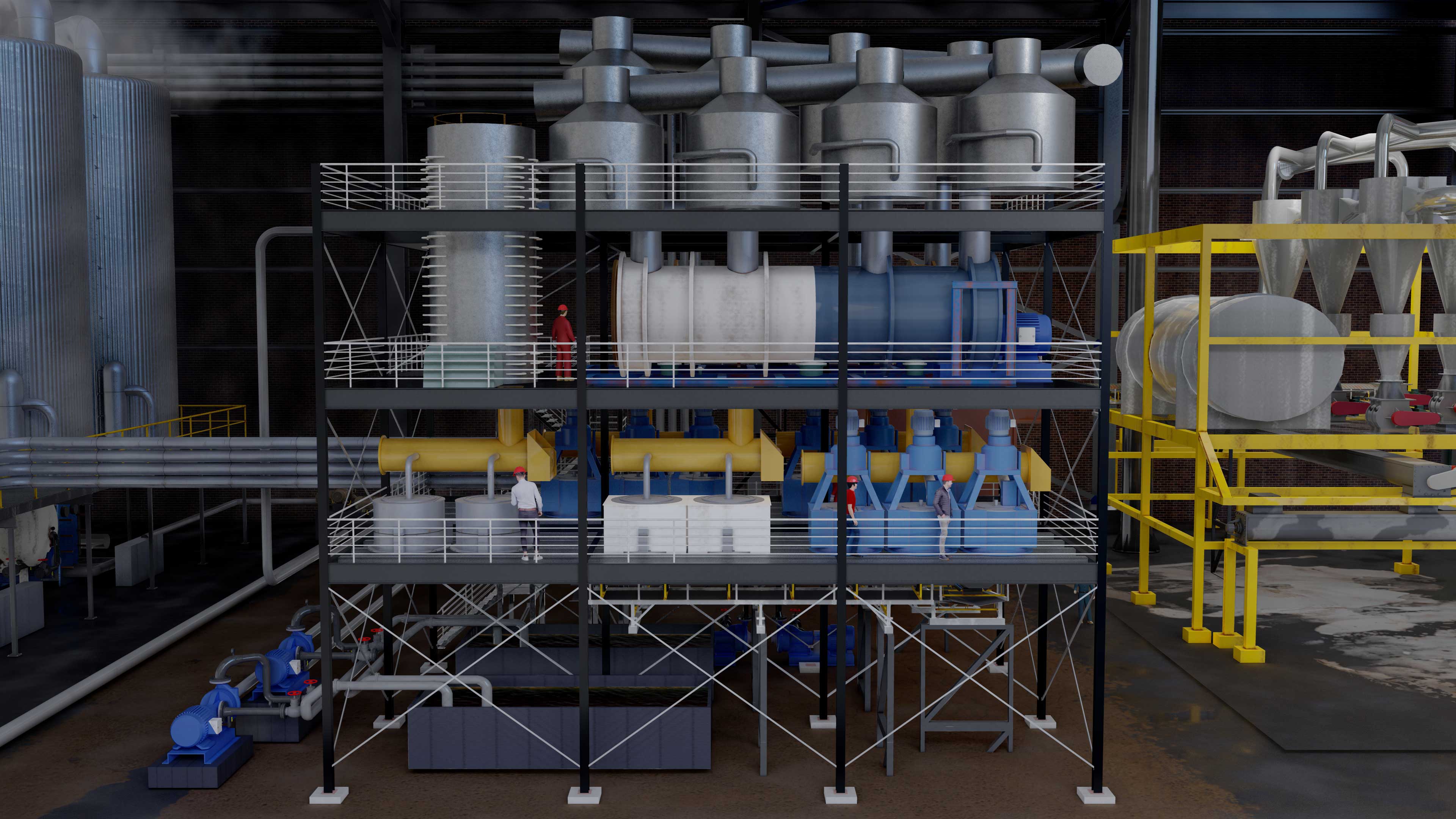
Vacuum Pan, Crystallization, Centrifuge
Thick juice is boiled and crystallized to a high concentration, mixed and dropped into centrifuges to separate the crystals from the liquor. Other sugars go through further processing.
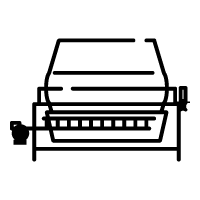
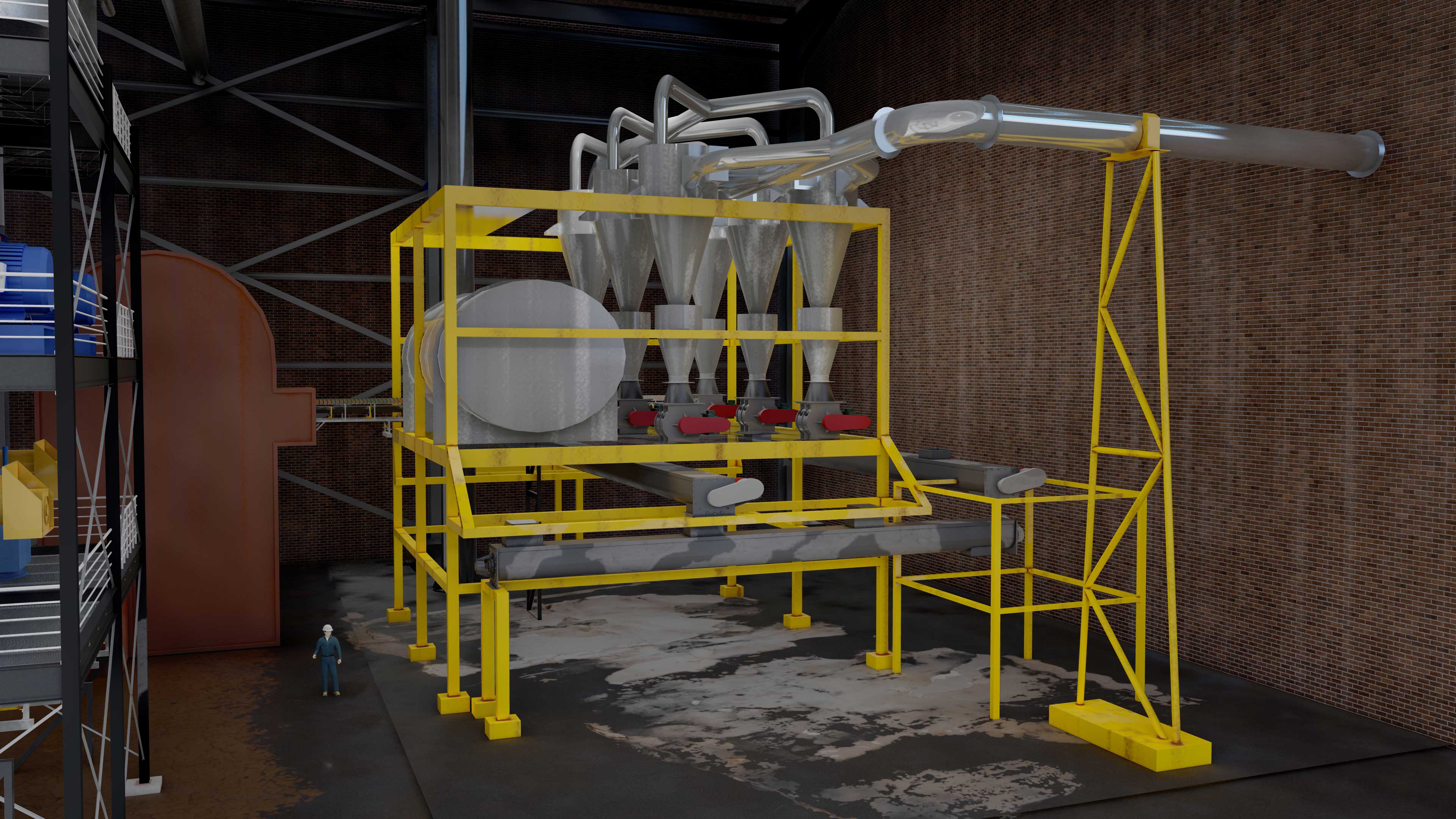
Drying/Storage
White sugar is then dried, cooled, and moved into storage silos until it is ready to be transported.
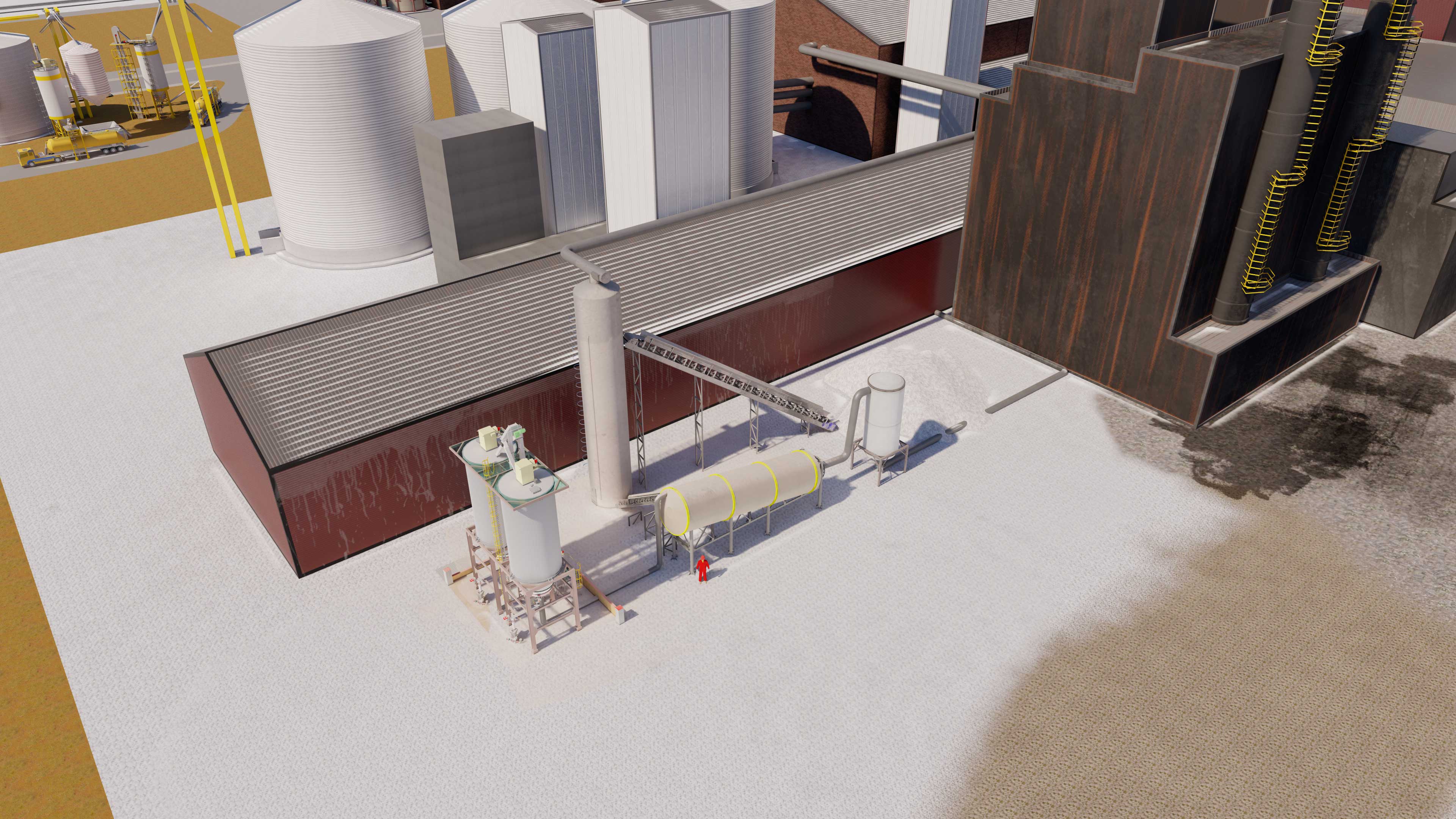
Lime Plant
Limestone and coal/natural gas are burned to produce CO2 gas and burned lime, and when mixed with water, produces milk of lime. These two products are used in purification during carbonation.
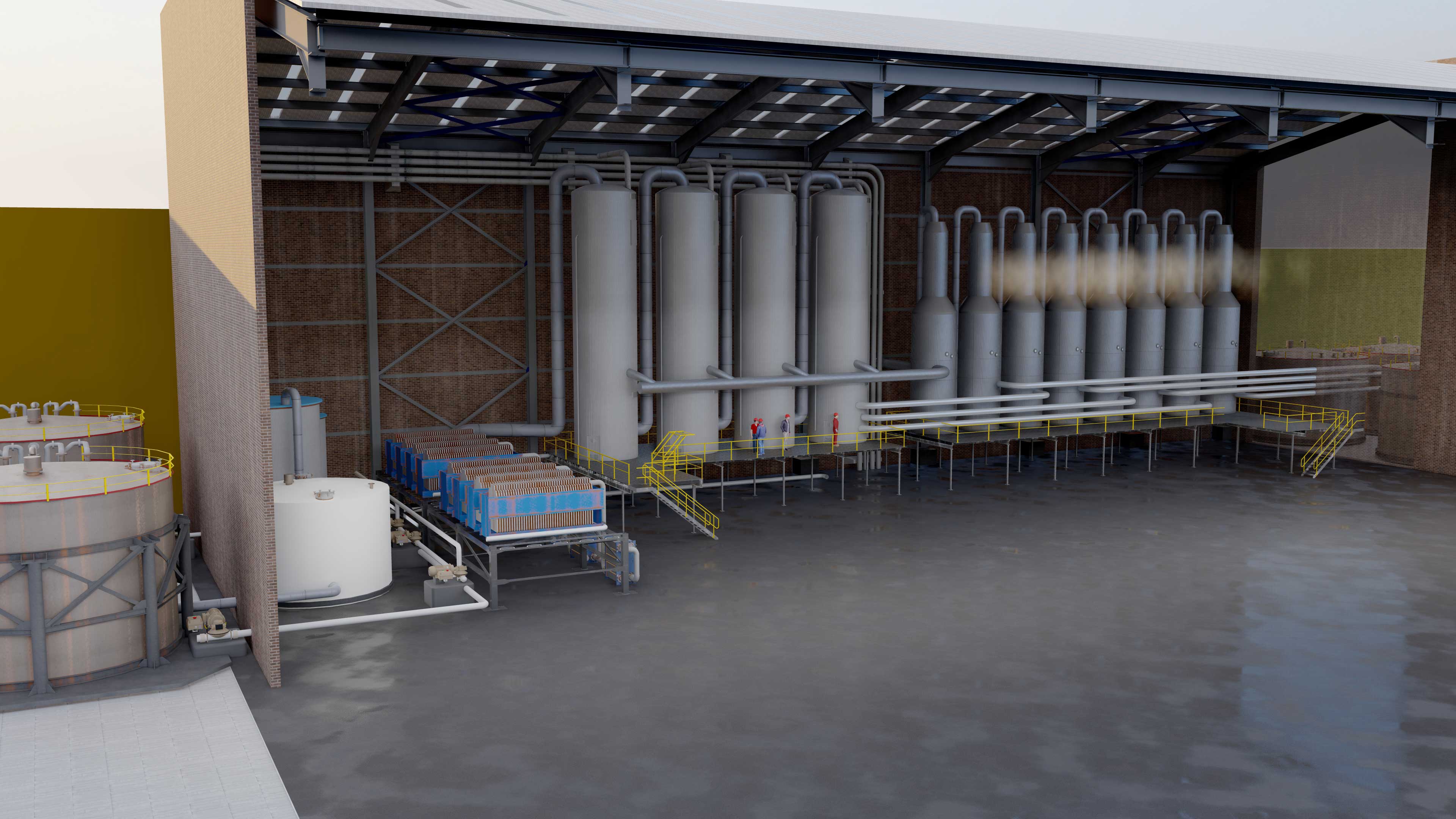
MDS Plant
Left over molasses is mixed with soda ash to form precipitate, which is then removed during filtration. Separation and evaporation then extracts and concentrates other by-products.
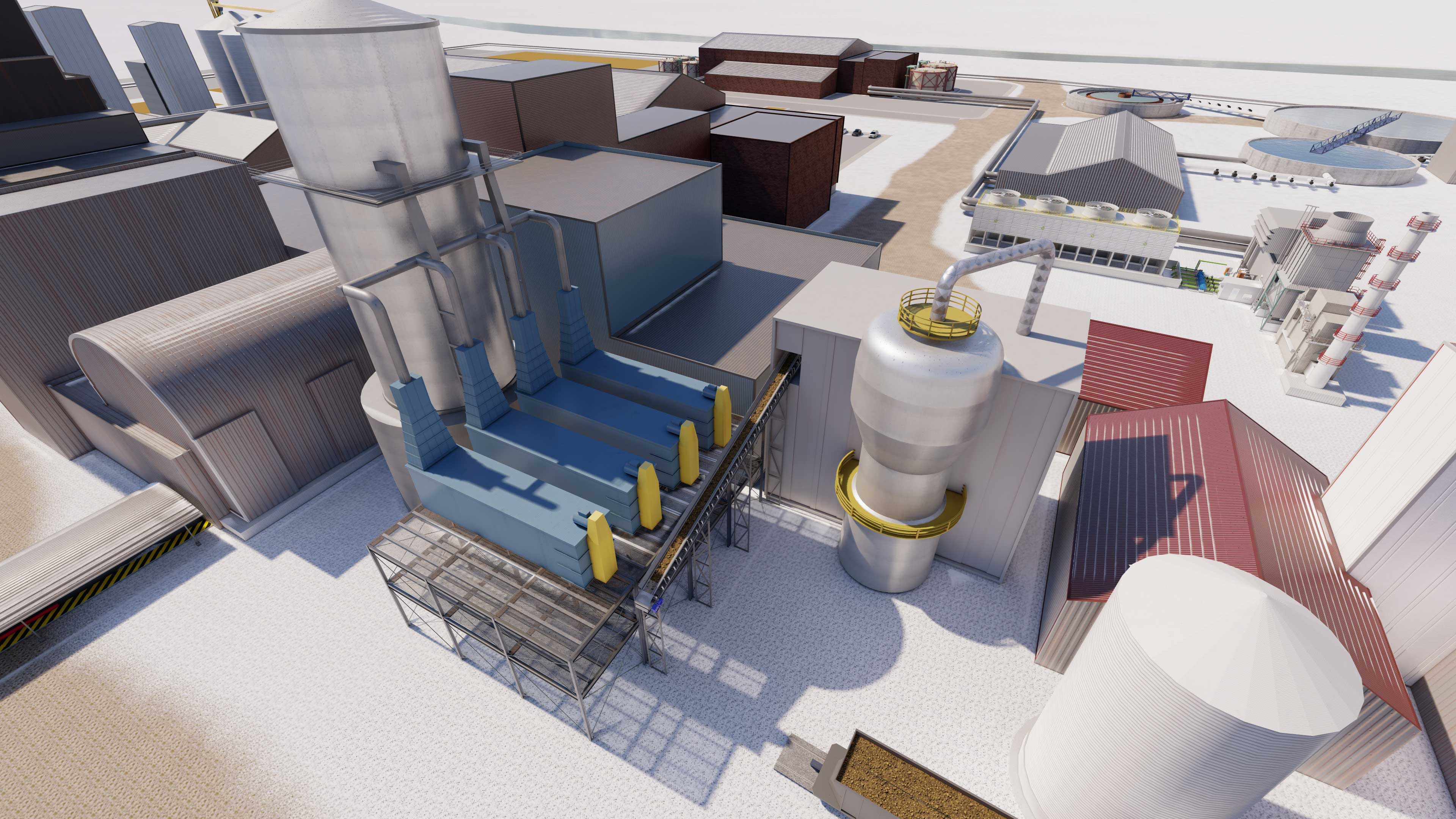
Pulp Drying / Pulp Press Spindle
Wet pulp is pressed to reduce moisture to about 75% then placed in dryer drums to be reduce moisture down to 10%. The dried pulp moves to the pellet mills, is compacted and goes to bulk storage.
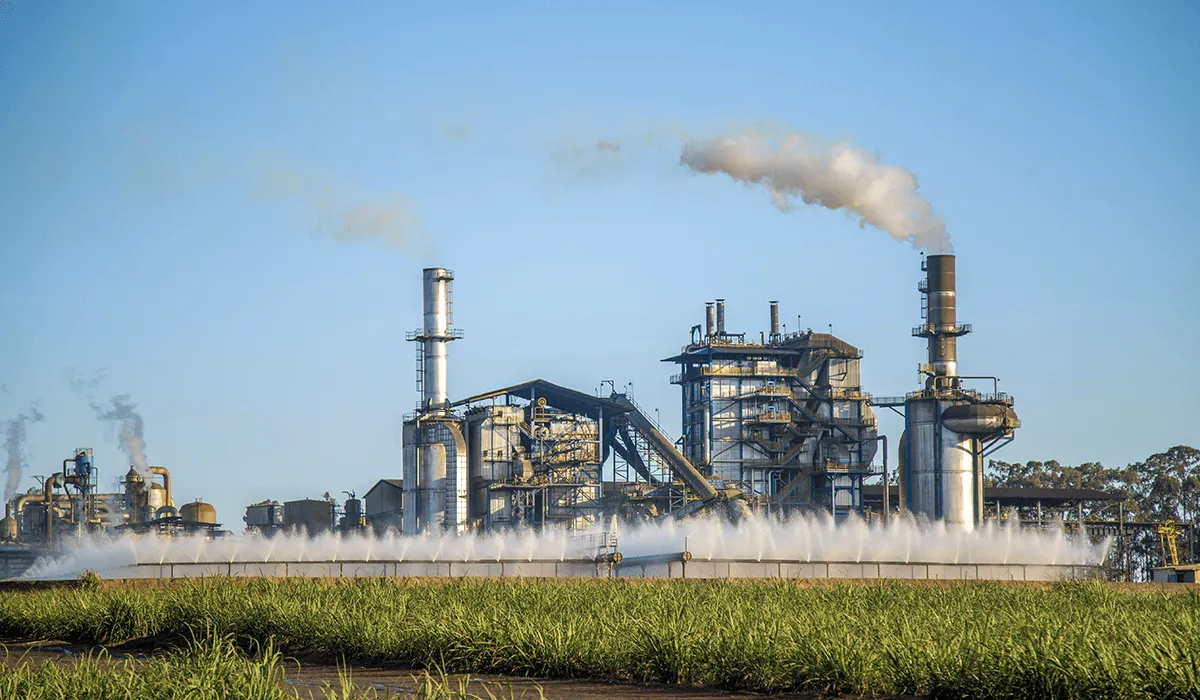
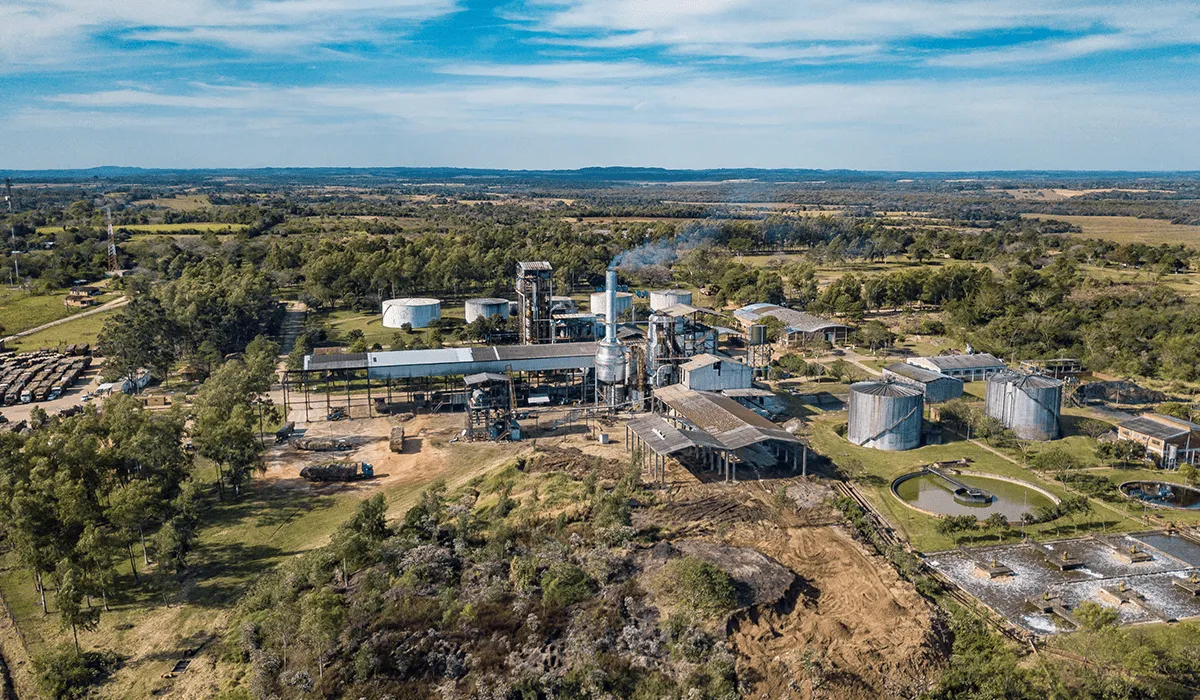
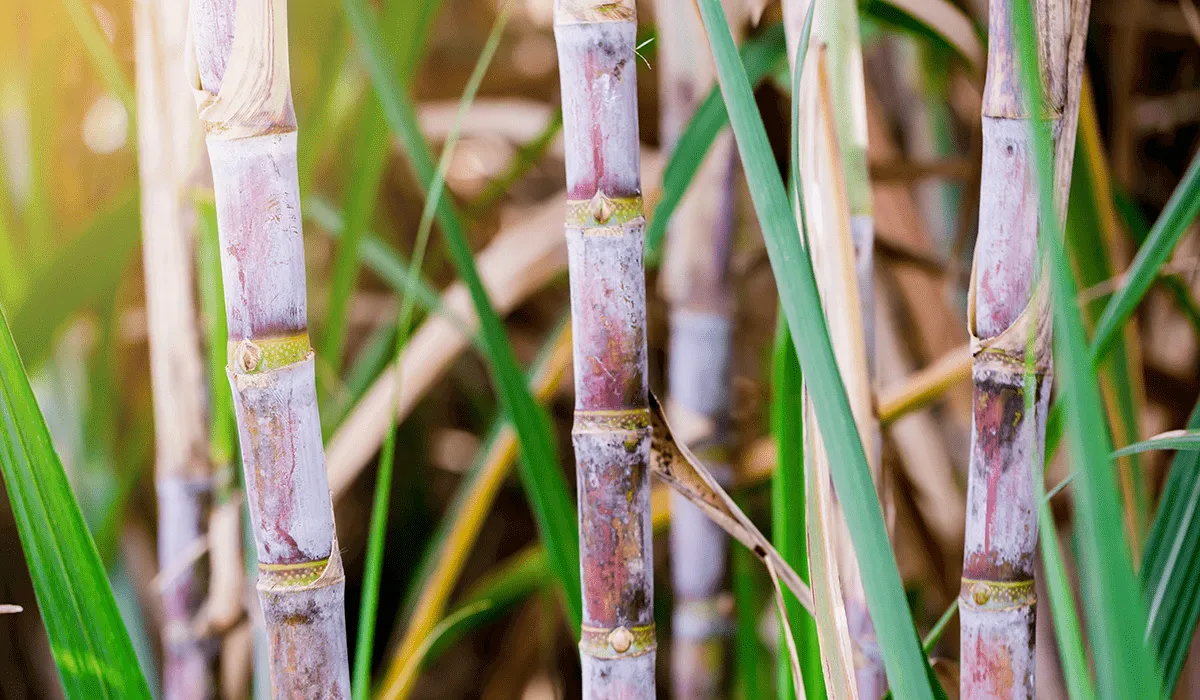
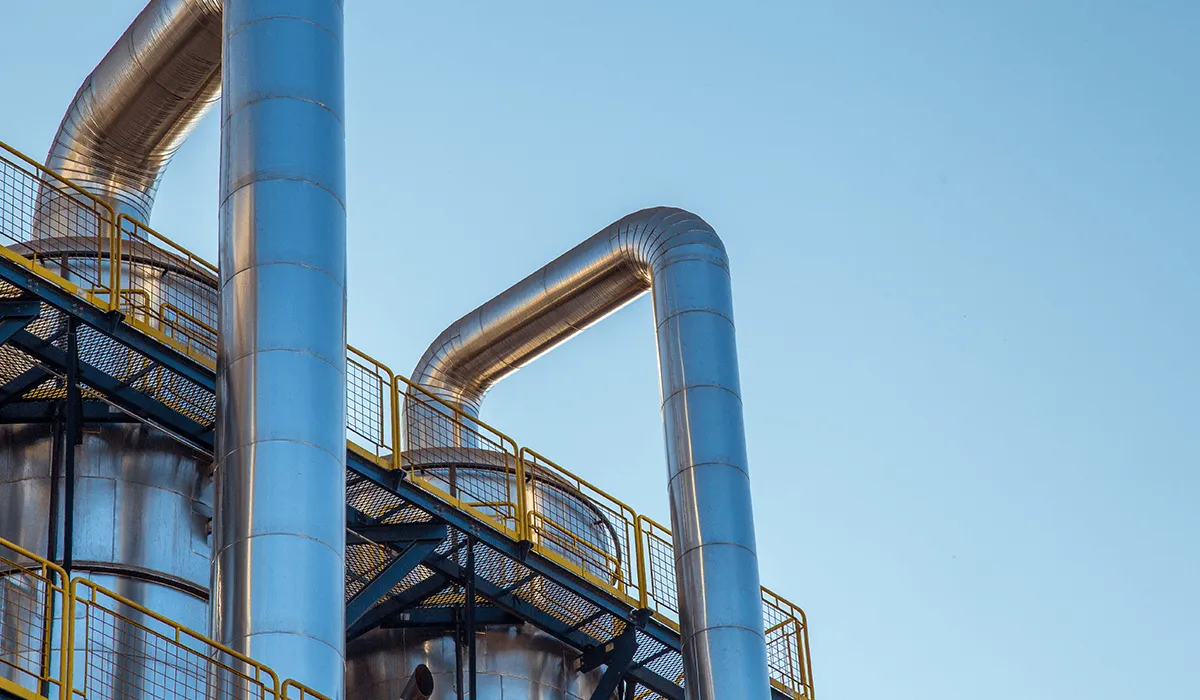
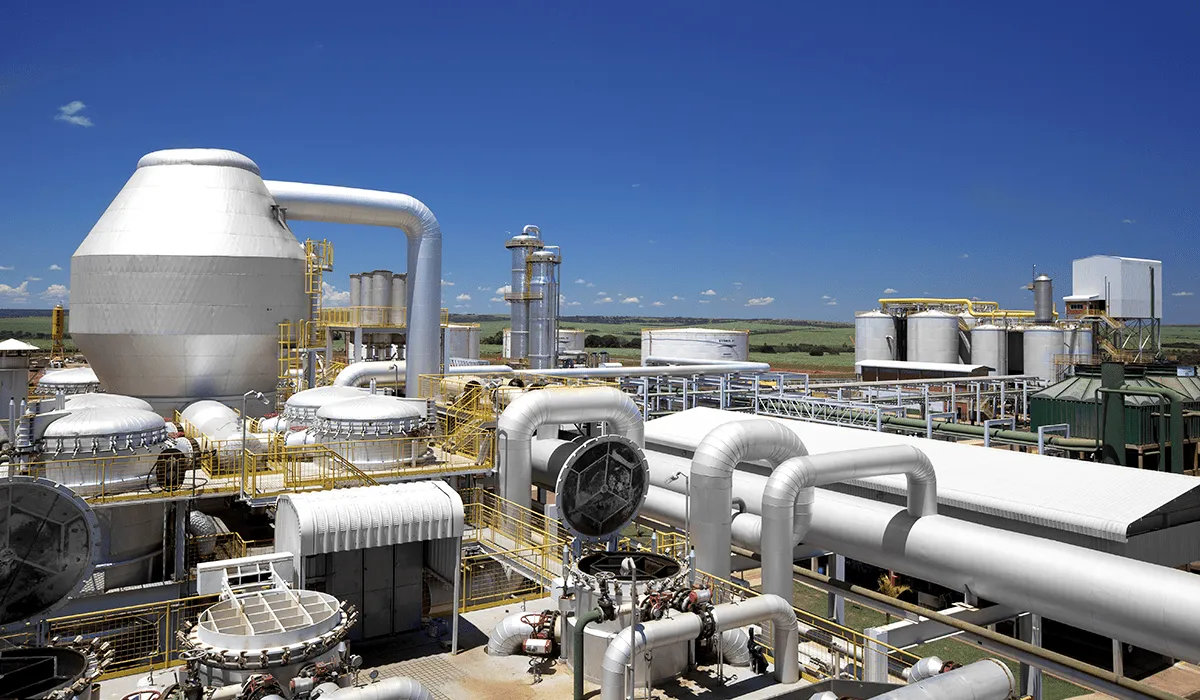
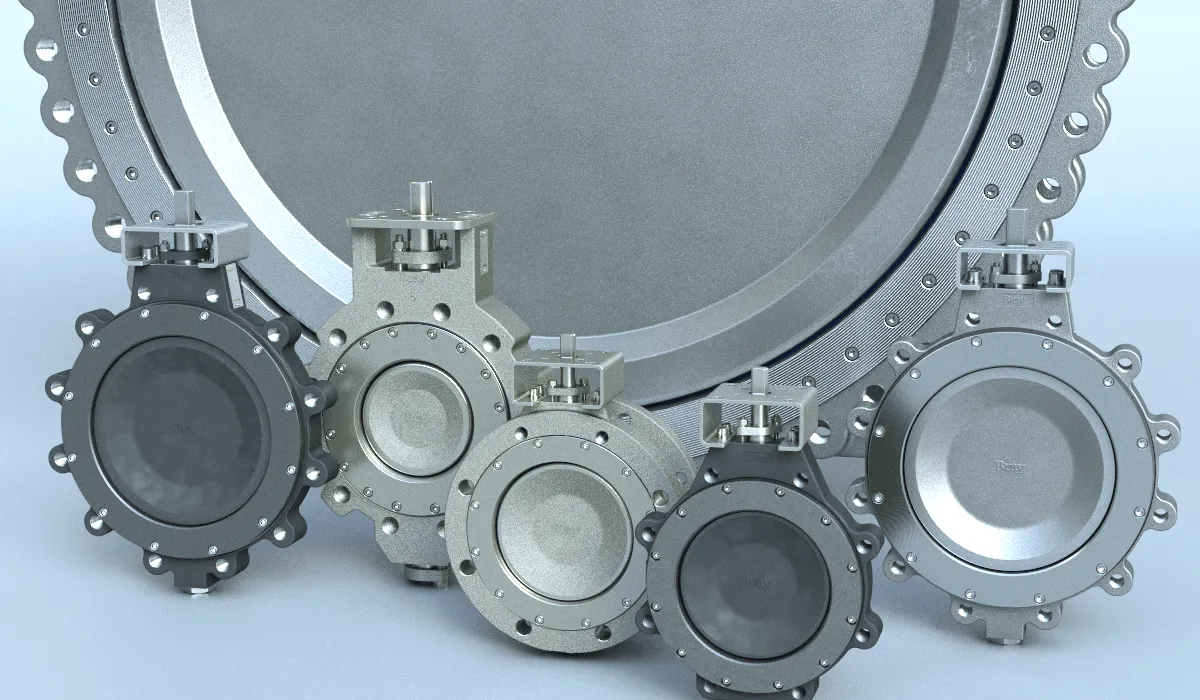
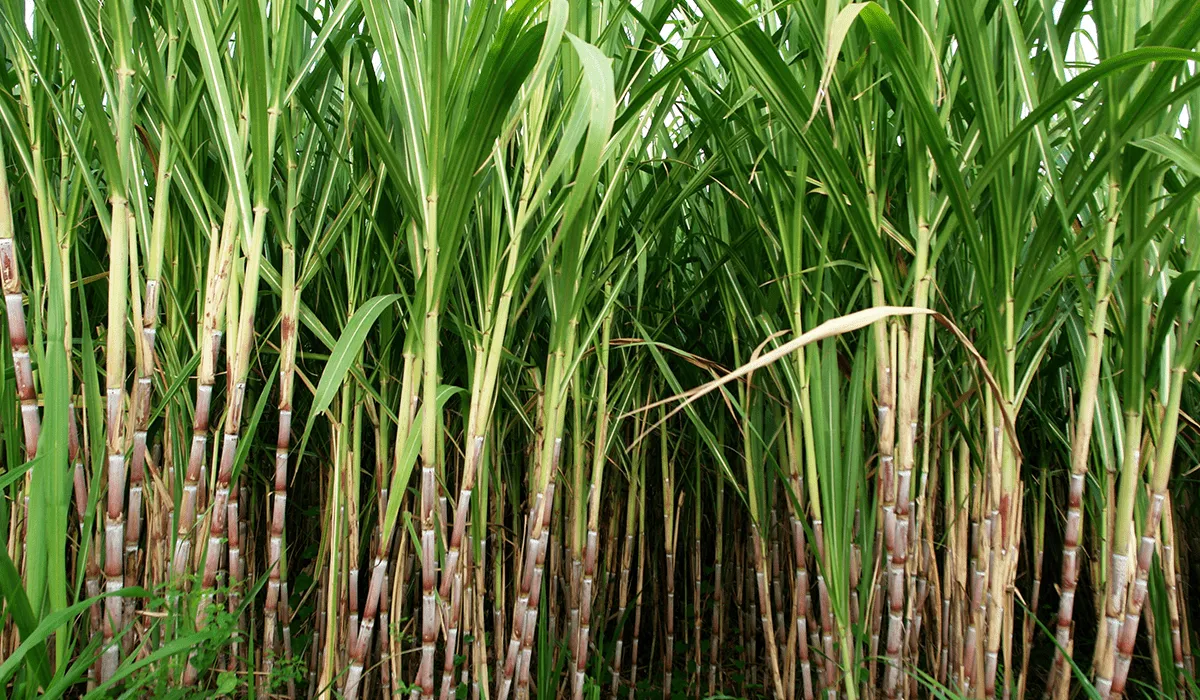
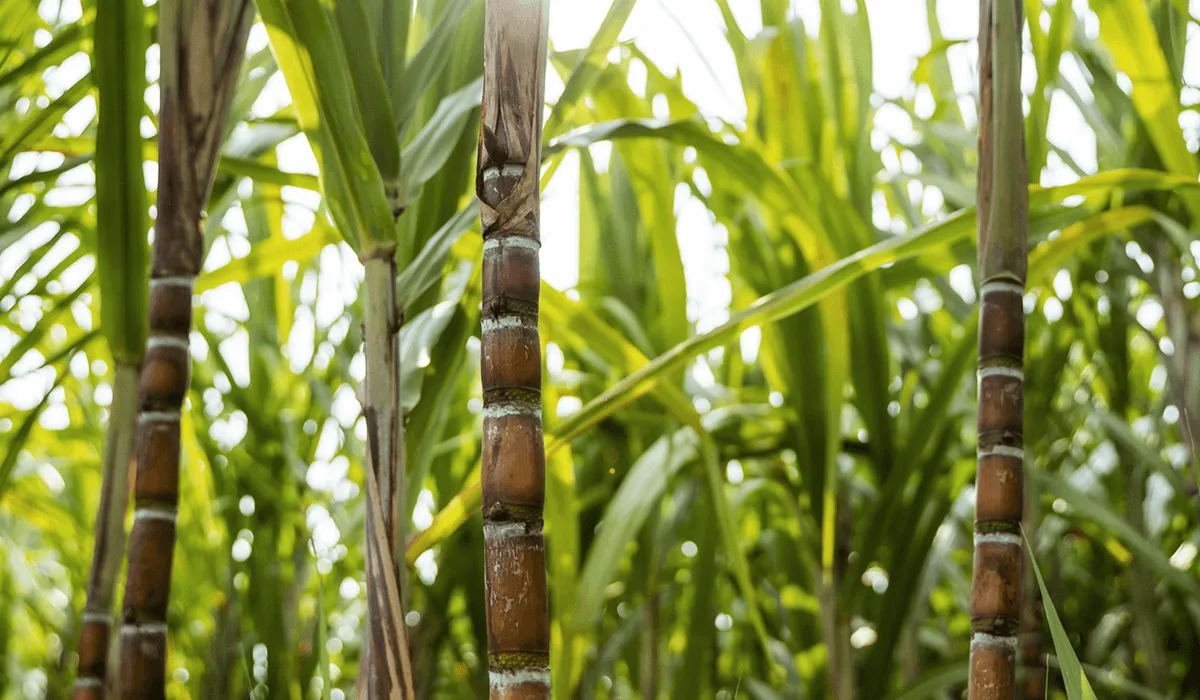
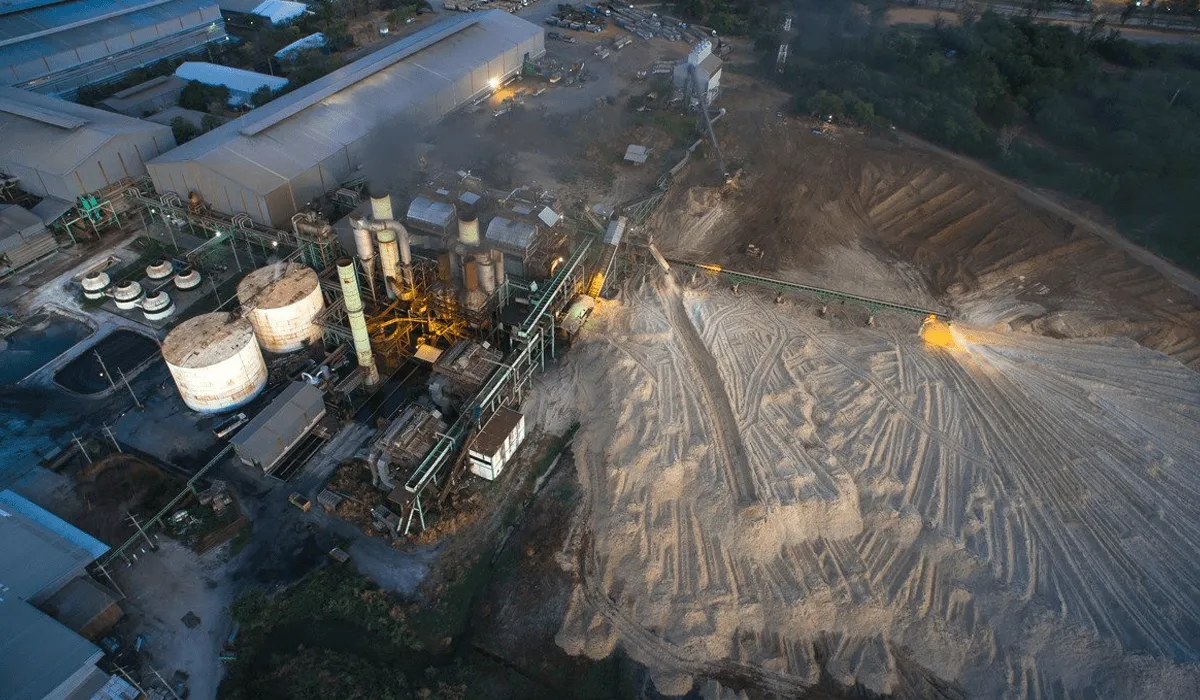
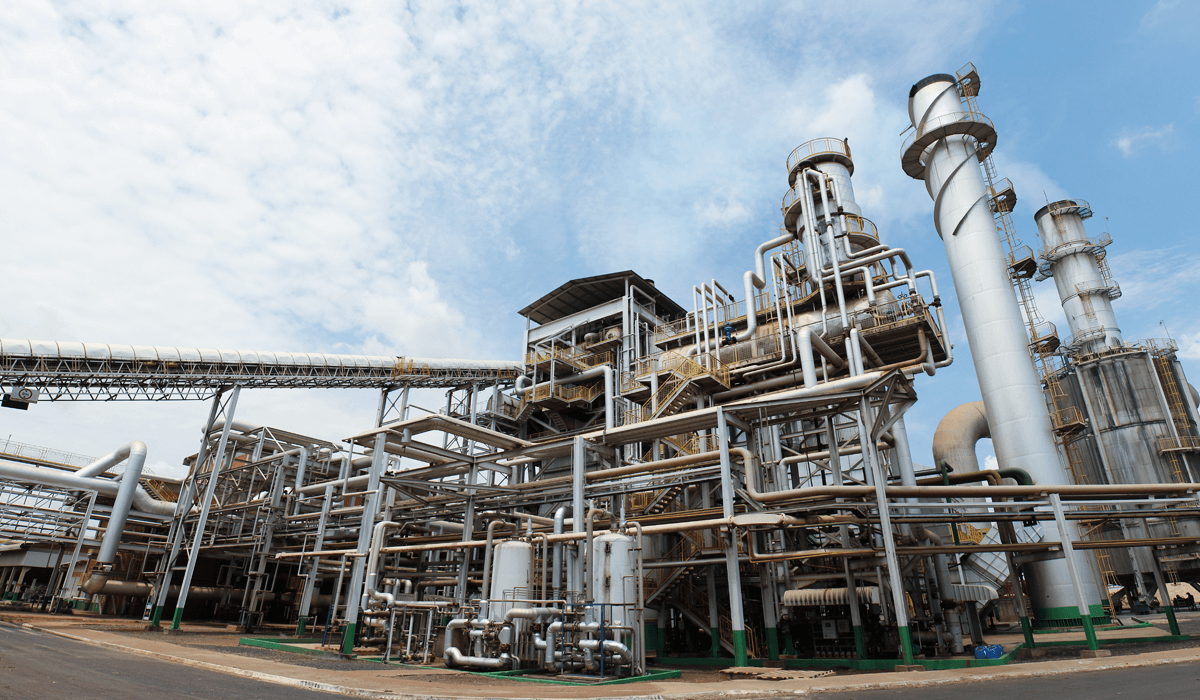